Autor: Reiner Bachthaler
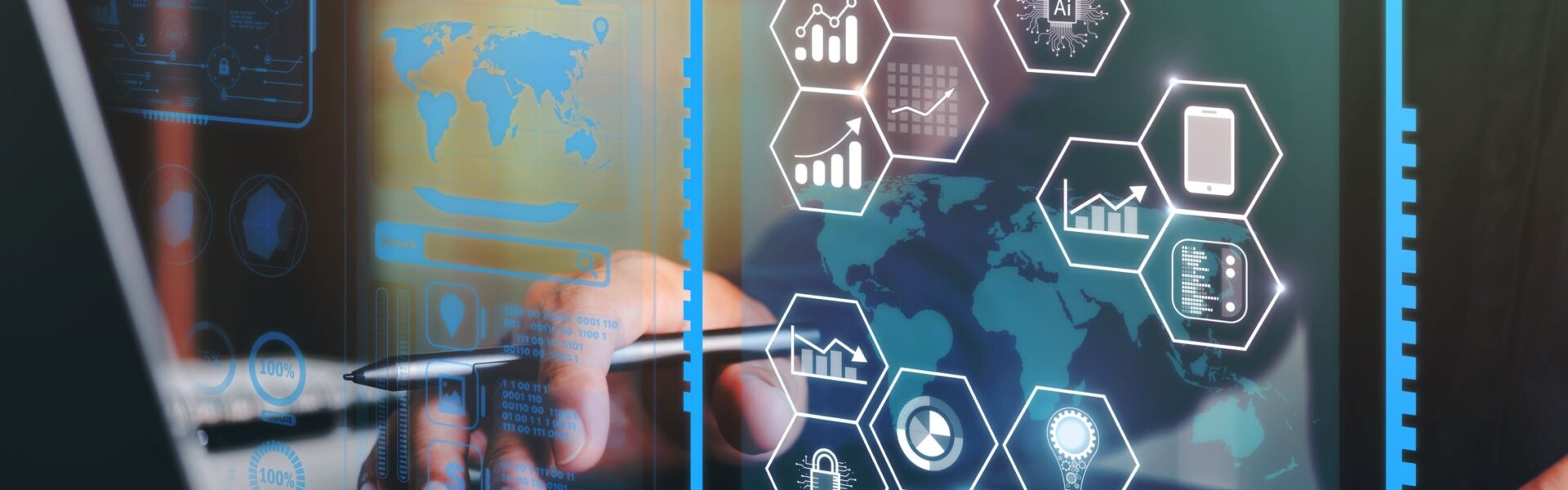
Werkslogistik in der Schüttgutindustrie
In der Werkslogistik der Schüttgutindustrie sind effiziente Prozesse eine Voraussetzung für den Erfolg. Gestörte Abläufe und Reibungsverluste können hingegen zu erheblichen Zeitverlusten oder teuren Fehlern bei der Abwicklung von Bestellungen führen.
Die mit der Werkslogistik in der Schüttgutindustrie zusammenhängenden Aufgaben sind vielschichtig, befassen sie sich doch mit allen Workflows rund um Beladung und Transport von Vor-, End- und Abfallprodukten für den Baustoffsektor. Das große Spektrum schafft somit viel Raum für mögliche Probleme, zugleich aber auch für Verbesserungen.
Um welche Branchen geht es?
Effiziente Prozesse sind für Unternehmen aus allen Sparten der Baustoffindustrie relevant. Unabhängig davon, ob es um Zement, Sand und Kies, Kalk, Asphalt oder Beton geht, die Anforderungen an eine kalkulierbare und effektive Abwicklung der Logistikaufgaben betreffen sämtliche Bereiche. Daher ist ein digitalisierter Logistikworkflow im Werk bzw. in den Werken für Unternehmen aus der Schüttgutbranche von herausragender Bedeutung.
Ein Prozessablauf, der schon vor dem Werkstor beginnt
Der gesamte Logistikworkflow in der Schüttgutindustrie beginnt schon weit vor dem Werkstor, lange bevor Lkw für die Beladung auf dem Werksgelände eintreffen. Die Stationen des Logistikworkflows umfassen:
- Bestellung des Kunden und Auftragserfassung beim Lieferanten
- Auftragsplanung und Abstimmung mit Disponenten
- Beauftragung von Spediteuren und zeitliche Ablaufplanung
- Ankunft, Check-in und Beladungsprozess im Werk
- Erstellung und Verwaltung von Lieferdokumenten sowie Check-out (im Werk)
- Tracking des Transportwegs ab Werk
- Auslieferung und Bestätigung durch den Empfänger
- Gegebenenfalls Nacherfassung von Zusatzaufwänden und -kosten
- Übertragung der der Informationen zu o.g. Abläufen an ERP oder Buchhaltungssysteme für die Abrechnung
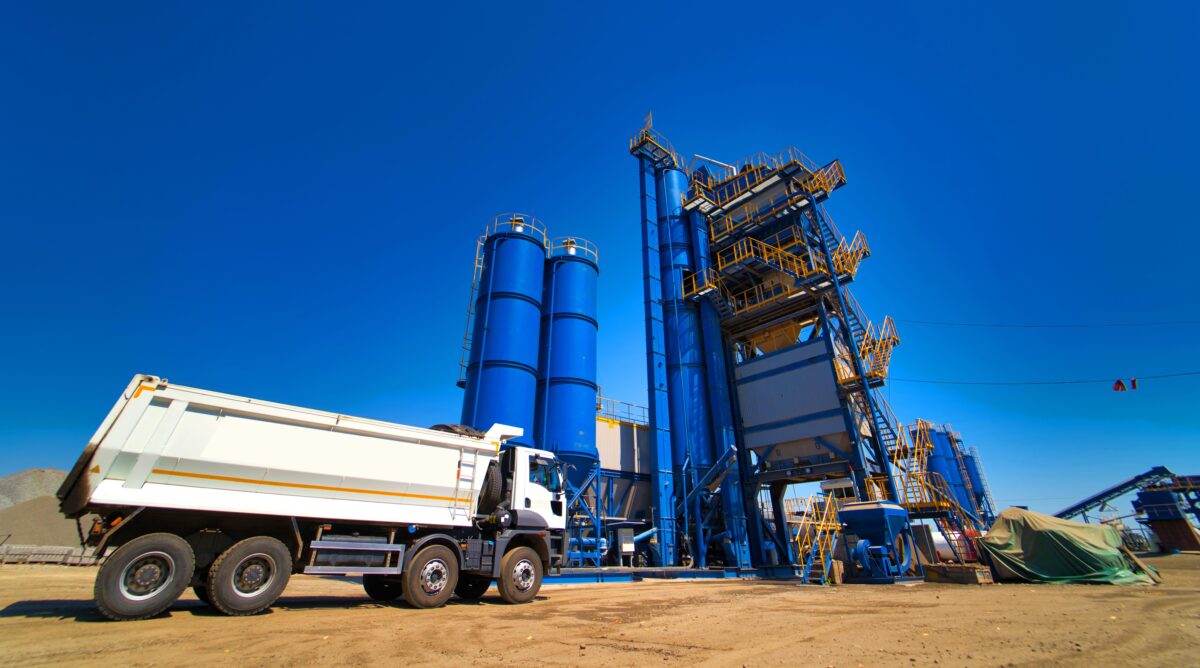
Dieser komplexe und vielschichtige Prozess stellt hohe Anforderungen an die vielen mit der Werkslogistik betrauten Parteien. So müssen Daten transparent ausgetauscht und konkrete Vorgaben für den reibungslosen Ablauf von Beladung und Transport getroffen werden. Dafür ist eine umfassende Koordination der Prozesse zwischen allen Beteiligten unerlässlich. Zu den Akteuren gehören:
- Auftraggeber (Kunde bzw. Zwischenhändler)
- Auftragserfasser und -planer beim Lieferanten
- Disponent beim Spediteur
- Lkw-Fahrer, der die Baustoffe abholt und ausliefert
- Personal des Lieferanten im Werk, das bei Bedarf den Check-in-/Check-out-Prozess und den Ladevorgang im Werk begleitet
- Materialempfänger (z.B. Mischwerke oder Baustellen)
Angesichts der vielen Beteiligten und der oft noch immer manuellen Bearbeitung der Daten besteht die Gefahr, dass Informationen nicht rechtzeitig übermittelt oder gar verloren gehen. Zudem können sich bei der Planung und dem häufig papiergestützten Datenaustausch Fehler einschleichen, was beim Logistikworkflow zu Verzögerungen und Zeitverlust führen kann.
Die Risiken eines manuellen Logistikworkflows in der Werkslogistik
Herkömmliche Prozesse im Logistikworkflow führen zu erhöhtem Kommunikationsbedarf zwischen Werkspersonal und Fahrern. Der damit zusammenhängende Aufwand beinhaltet Risiken für eine funktionierende Werkslogistik. Diese können am Werkstor, bei der Verladung, beim Check-out oder beim Tracking des Transports auftreten.
Ein typischer Fall ist, dass der Lkw-Fahrer beim Eintreffen am Werk unzureichende, keine oder falsche Informationen zu seiner Lieferung hat.
Mögliche Folgen:
- Verzögerung bei der Werkseinfahrt
- Hohe, manuelle Aufwände für das Werkspersonal
- Lkw blockieren die Einfahrtswaage
- Erhöhung der Lkw-Durchlaufzeit
Auch auf dem Werksgelände folgen durch den manuellen Prozess Probleme durch
- Begrenzte Slots bei der Beladung
- Gegebenenfalls Fehlbeladungen
- Verzögerungen bei der Lkw-Abfertigung
Bei der Abfahrt der Lkw schließlich führt die manuelle Übermittlung des Lieferscheins zu
- Verzögerung bei der Werksausfahrt
- Verlängerung der Transportzeit
- Vermeidbaren CO2 Belastungen durch Ausdrucke
Es zeigt sich also, dass aus den aufwendigen manuellen Prozessen erhebliche Zeitverluste und Zusatzkosten für alle am Logistikworkflow beteiligten Akteure entstehen.
Mit VAS Yard Management zum automatisierten und effizienten Logistikworkflow
Die Antwort auf die geschilderten Herausforderungen bietet ein digitaler, skalierbarer und voll integrierter Lösungsansatz. Dieser macht Aufwand und Kosten in der Werkslogistik beherrschbar und lässt sich punktgenau an die jeweiligen Anforderungen und Ressourcen im Unternehmen anpassen. Ein gutes Beispiel für eine solche Lösung ist das VAS Yard Management, eine an die jeweiligen Kundenanforderungen angepasste skalierbare Logistiklösung, die aus bewährten Standardmodulen, Customizing und Schnittstellen zu anderen Softwaresystem und Hardware besteht. Die Basis zum erfolgreichen Einsatz dieser Lösung ist ein professionelles Consulting, um eine optimal auf die Anforderungen des jeweiligen Kunden angepasste Lösung zu erreichen. Es wurde speziell für die Bedürfnisse der Schüttgutindustrie im Baustoffbereich entwickelt, wo es die Logistik- und Verladeprozesse im Werk nachhaltig optimiert.
VAS Yard Management deckt alle Abläufe der Abfertigung von Fahrzeugen im Werk und viele weitere Logistikanwendungen ab. Dies reicht von der Eingabe der Anmeldedaten für den Sicherheitscheck bei der Werkseinfahrt über Verwiegung, Verladung und anschließende Ausstellung von Versandpapieren bis zur kontrollierten Werksausfahrt.
Eine umfassende Lösung auch über das Produktionswerk hinaus wird durch die Integration des zentralen Logistikworkflows durch VAS Cloud Logistics erreicht. Damit können auch zentrale Prozesse wie z.B. Bestellung sowie Auftrags- und Transportplanung schnell und komfortabel durchgeführt werden.
Wie der digitalisierte Logistikworkflow funktioniert
Der digitale Workflow mit VAS Yard Management umfasst den gesamten Ablauf der Werkslogistik:
- Fahrzeugidentifikation mit flexiblen ID-Checks (RF/ID Karten, kamerabasierte Kennzeichenerkennung, QR-Codes)
- Automatisierte Einfahrt: Check-in am Self-Service-Terminal oder per App, ohne dass der Fahrer aussteigen muss
- Einfahrtsverwiegung: Messung des Eingangsgewichts des Lkw
- Weiterleitung an Verladestation
- Automatisierter Ladeprozess– optional mit direkter Ermittlung der exakten IST-Menge an der Ladestation
- Weiterleitung zur Werksausfahrt
- Ausfahrtsverwiegung: Messung des Ausgangsgewichts des Lkw
- Ausfahrtsprozess: Fahrer erhält Ladepapiere (optional auch papierlos mit automatischer elektronischer Lieferdatenübertragung) am Self-Service-Check-out
- Anschließend: Auswertungen und Analyse der einzelnen Vorgänge sowie aggregiert über einen längeren Zeitraum
Dieser Workflow verdeutlicht, wie VAS Yard Management die Optimierung der Werkslogistik nachhaltig unterstützt und die Prozesse für alle Beteiligten effizienter gestaltet. So gelingen Abläufe wie z. B. die mobile Beladung von Radladern für Schüttgut oder von Gabelstaplern für Sackware mithilfe der vernetzten VAS Terminals reibungslos, da aufwändige manuelle Abläufe durch digitale Prozesse abgelöst und damit verschlankt werden.
Außerdem kann dank der digitalen Verwaltung von Ladestellen bei jedem Lkw individuell leicht festgelegt werden, wo dieser beladen werden soll. Zusätzliche Flexibilität erhält die Lösung durch die Unterstützung von Verladungen auf der Schiene oder von speziell für Deponien definierten Anlieferprozessen.
Über die operativen Erleichterungen hinaus bietet die VAS Werkslogistik für Unternehmen zahlreiche weitere Vorteile. So ist die Yard Management-Software von Axians IAS hochgradig skalierbar und kann modular an die individuellen Kundenanforderungen angepasst werden. Zudem verfügt die Lösung über eine hohe Integrationsfähigkeit, wodurch die Anbindung an vor- und nachgeschaltete Systeme (z.B. ERP) zur umfassenden Synchronisierung von Aufträgen, Lieferungen und Stammdaten gewährleistet wird.
Zusammenfassung:
Was der zentrale Logistikworkflow bringt
Der digitalisierte Workflow in der Werkslogistik trägt bei allen Akteuren und Prozessen zur Steigerung der Produktivität bei. Neben den Baustoffproduzenten profitieren von den verschlankten Prozessen auch Lieferanten, Auftragsplaner und Disponenten, Fahrer sowie die Empfänger des Materials. Die Datentransparenz verschafft den Unternehmen umfassenden Überblick und damit beste Voraussetzungen für die spätere Analyse.
Die Vorteile auf einen Blick
Manuelle Tätigkeiten werden für alle Akteure nachhaltig gesenkt. Das automatische Handling sorgt für geringere Aufwände und Fehlerraten, was zusätzlich Kosten spart.
Das datenbasierte (durchgängige und konsistente Daten-) Modell versorgt die Beteiligten rechtzeitig mit allen relevanten Daten, was schnellere Bestell- und Lieferprozesse ermöglicht.
Die Softwareunterstützung schließt fehlerhafte manuelle Eingaben aus. Eine automatische Statuskontrolle sowie transparente und konsistente Daten gewährleisten eine hohe Prozesssicherheit.
Mit der Digitalisierung und Automatisierung entfällt ein Großteil der manuellen Prozesse bei Einfahrt und Ausfahrt, dem Wiegen und der Beladung der Lkw.
Ablauf eines erfolgreichen Automatisierungsprojekts
Um die Automatisierung in der Werkslogistik effizient zu gestalten, ist eine präzise Planung des Projekts unabdingbar. Dazu gehört die initiale Erfassung von Anforderungen und Zielen in enger Abstimmung zwischen Auftraggeber und Dienstleister. Nach eingehender Analyse erfolgt dann die Priorisierung der einzelnen Projektschritte.
Bei der anschließenden Umsetzung wird anhand von regelmäßigen Soll-Ist-Vergleichen gewährleistet, dass Priorisierung und Plan eingehalten werden, beziehungsweise dass diese bei Bedarf angepasst werden. Auch hier ist die umfassende Kommunikation zwischen allen Beteiligten unabdingbar, um Reibungsverluste zu vermeiden.
Voraussetzung für den Projekterfolg ist ein kompetenter Begleiter, der die Automatisierung der Werkslogistik mit seinem Know-how während aller Phasen unterstützt. Mit optionalen Zusatzlösungen wie Cloud Logistics, App-Entwicklungen und maßgeschneiderten Consulting-Services bietet das Team von Axians IAS all dies aus einer Hand.
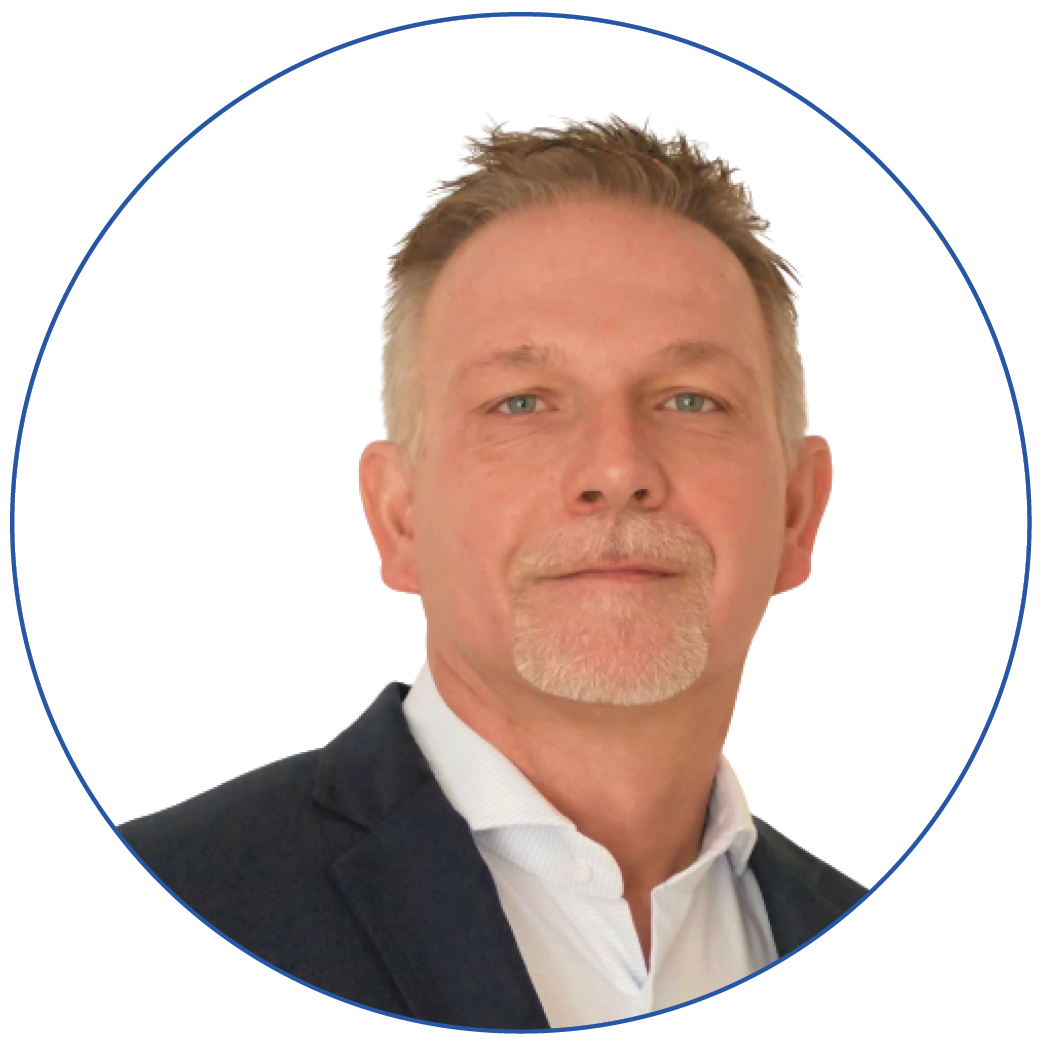
Reiner Bachthaler
Senior Produktmanager
Interesse? Dann wenden Sie sich gerne an uns.
Sie sehen gerade einen Platzhalterinhalt von HubSpot. Um auf den eigentlichen Inhalt zuzugreifen, klicken Sie auf die Schaltfläche unten. Bitte beachten Sie, dass dabei Daten an Drittanbieter weitergegeben werden.
Mehr Informationen