Author: Reiner Bachthaler
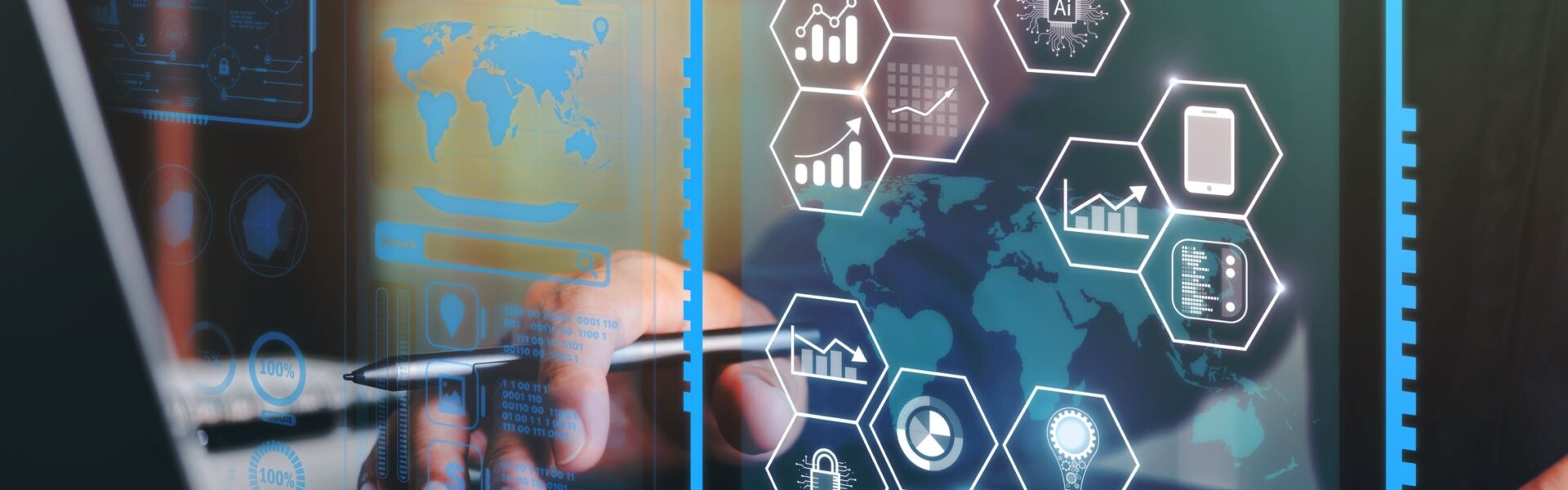
Plant logistics in the bulk goods industry
Efficient processes are a prerequisite for success in plant logistics in the bulk goods industry. Disrupted processes and frictional losses, on the other hand, can lead to considerable time losses or costly errors when processing orders.
The tasks associated with plant logistics in the bulk materials industry are complex, as they deal with all workflows relating to the loading and transportation of primary, end and waste products for the construction materials sector. The broad spectrum therefore creates plenty of scope for potential problems, but also for improvements.
Which sectors are involved?
Efficient processes are relevant for companies from all sectors of the building materials industry. Regardless of whether cement, sand and gravel, lime, asphalt or concrete are involved, the requirements for calculable and effective handling of logistics tasks apply to all areas. A digitalized logistics workflow in the plant or plants is therefore of paramount importance for companies in the bulk goods industry.
A process flow that starts before the factory gate
The entire logistics workflow in the bulk goods industry begins well before the factory gate, long before trucks arrive on site for loading. The stations of the logistics workflow include:
- Customer order and order entry at the supplier
- Order planning and coordination with dispatchers
- Commissioning of freight forwarders and scheduling
- Arrival, check-in and loading process at the plant
- Creation and management of delivery documents and check-out (in the factory)
- Tracking the transport route ex works
- Delivery and confirmation by the recipient
- If necessary, subsequent recording of additional expenses and costs
- Transfer of information on the above processes to ERP or accounting systems for billing purposes
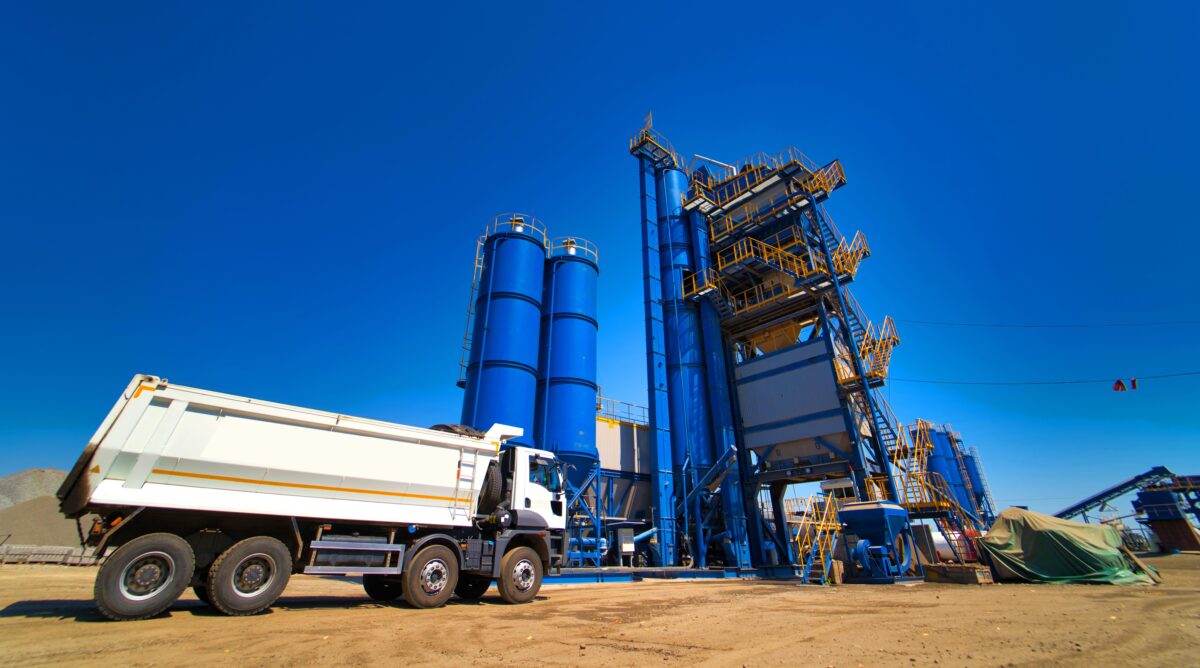
This complex and multi-layered process places high demands on the many parties involved in plant logistics. Data must be exchanged transparently and concrete specifications must be made for the smooth flow of loading and transportation. Comprehensive coordination of processes between all parties involved is essential for this. The players include:
- Client (customer or intermediary)
- Order compiler and planner at the supplier
- Dispatcher at the freight forwarder
- Truck driver who collects and delivers the building materials
- Supplier personnel at the plant to accompany the check-in/check-out process and the loading process at the plant if required
- Material recipients (e.g. mixing plants or construction sites)
In view of the large number of parties involved and the fact that data is often still processed manually, there is a risk that information will not be transmitted on time or may even be lost. In addition, errors can creep in during planning and the often paper-based data exchange, which can lead to delays and loss of time in the logistics workflow.
The risks of a manual logistics workflow in plant logistics
Conventional processes in the logistics workflow lead to an increased need for communication between plant personnel and drivers. The associated costs entail risks for functioning plant logistics. These can occur at the factory gate, during loading, at check-out or during transportation tracking.
A typical case is that the truck driver has insufficient, no or incorrect information about his delivery when he arrives at the plant.
Possible consequences:
- Delay at the plant entrance
- High manual effort for plant personnel
- Trucks block the entrance weighbridge
- Increase in truck throughput time
The manual process also causes problems on the factory premises due to
- Limited slots for loading
- Incorrect loads, if applicable
- Delays in truck dispatch
Finally, when the trucks depart, the manual transmission of the delivery bill leads to
- Delay at the factory exit
- Extension of the transport time
- Avoidable CO2 emissions from printouts
It can therefore be seen that the time-consuming manual processes result in considerable time losses and additional costs for all those involved in the logistics workflow.
Automated and efficient logistics workflow with VAS Yard Management
The answer to the challenges described is a digital, scalable and fully integrated solution approach. This makes effort and costs in plant logistics manageable and can be adapted precisely to the respective requirements and resources in the company. A good example of such a solution is VAS Yard Management, a scalable logistics solution that is adapted to the respective customer requirements and consists of proven standard modules, customizing and interfaces to other software systems and hardware. The basis for the successful use of this solution is professional consulting in order to achieve a solution that is optimally adapted to the requirements of the respective customer. It was developed specifically for the needs of the bulk materials industry in the building materials sector, where it sustainably optimizes logistics and loading processes in the factory.
VAS Yard Management covers all processes for handling vehicles in the plant and many other logistics applications. This ranges from entering the registration data for the security check at the plant entrance to weighing, loading and the subsequent issue of shipping documents through to the controlled plant exit.
A comprehensive solution that extends beyond the production plant is achieved by integrating the central logistics workflow with VAS Cloud Logistics. This means that central processes such as ordering and order and transport planning can also be carried out quickly and conveniently.
How the digitalized logistics workflow works
The digital workflow with VAS Yard Management covers the entire plant logistics process:
- Vehicle identification with flexible ID checks (RF/ID cards, camera-based license plate recognition, QR codes)
- Automated entry: check-in at the self-service terminal or via app without the driver having to get out of the vehicle
- Entry weighing: Measurement of the incoming weight of the truck
- Forwarding to loading station
- Automated charging process – optionally with direct determination of the exact ACTUAL quantity at the charging station
- Forwarding to the factory exit
- Exit weighing: Measurement of the initial weight of the truck
- Exit process: driver receives loading documents (optionally also paperless with automatic electronic delivery data transfer) at the self-service check-out
- Subsequently: Evaluations and analysis of individual processes as well as aggregated over a longer period of time
This workflow illustrates how VAS Yard Management sustainably supports the optimization of plant logistics and makes processes more efficient for everyone involved. Processes such as the mobile loading of wheel loaders for bulk goods or forklift trucks for bagged goods run smoothly with the help of the networked VAS terminals, as time-consuming manual processes are replaced by digital processes and thus streamlined.
In addition, thanks to the digital management of loading points, it is easy to determine individually for each truck where it should be loaded. The solution gains additional flexibility by supporting rail loading or delivery processes specially defined for landfills.
In addition to operational simplifications, VAS plant logistics offers companies numerous other advantages. The yard management software from Axians IAS is highly scalable and can be modularly adapted to individual customer requirements. The solution also has a high level of integration capability, which ensures connection to upstream and downstream systems (e.g. ERP) for comprehensive synchronization of orders, deliveries and master data.
Summary:
What the central logistics workflow brings
The digitalized workflow in plant logistics helps to increase productivity for all players and processes. In addition to the building material producers, suppliers, order planners and dispatchers, drivers and the recipients of the material also benefit from the streamlined processes. Data transparency provides companies with a comprehensive overview and thus the best conditions for subsequent analysis.
The advantages at a glance
Manual activities are sustainably reduced for all stakeholders. Automatic handling reduces the workload and error rates, which also saves costs.
The data-based (end-to-end and consistent data) model provides the parties involved with all relevant data in good time, which enables faster ordering and delivery processes.
The software support excludes incorrect manual entries. Automatic status monitoring and transparent and consistent data ensure a high level of process reliability.
Digitalization and automation have eliminated a large part of the manual processes involved in entering and exiting, weighing and loading trucks.
Process of a successful automation project
Precise project planning is essential for efficient automation in plant logistics. This includes the initial recording of requirements and objectives in close coordination between the client and service provider. After a detailed analysis, the individual project steps are prioritized.
During subsequent implementation, regular target/actual comparisons are used to ensure that the prioritization and plan are adhered to and that they are adjusted if necessary. Here too, comprehensive communication between all parties involved is essential in order to avoid frictional losses.
A prerequisite for project success is a competent partner who supports the automation of plant logistics with their expertise during all phases. With optional add-on solutions such as cloud logistics, app development and customized consulting services, the Axians IAS team offers all of this from a single source.
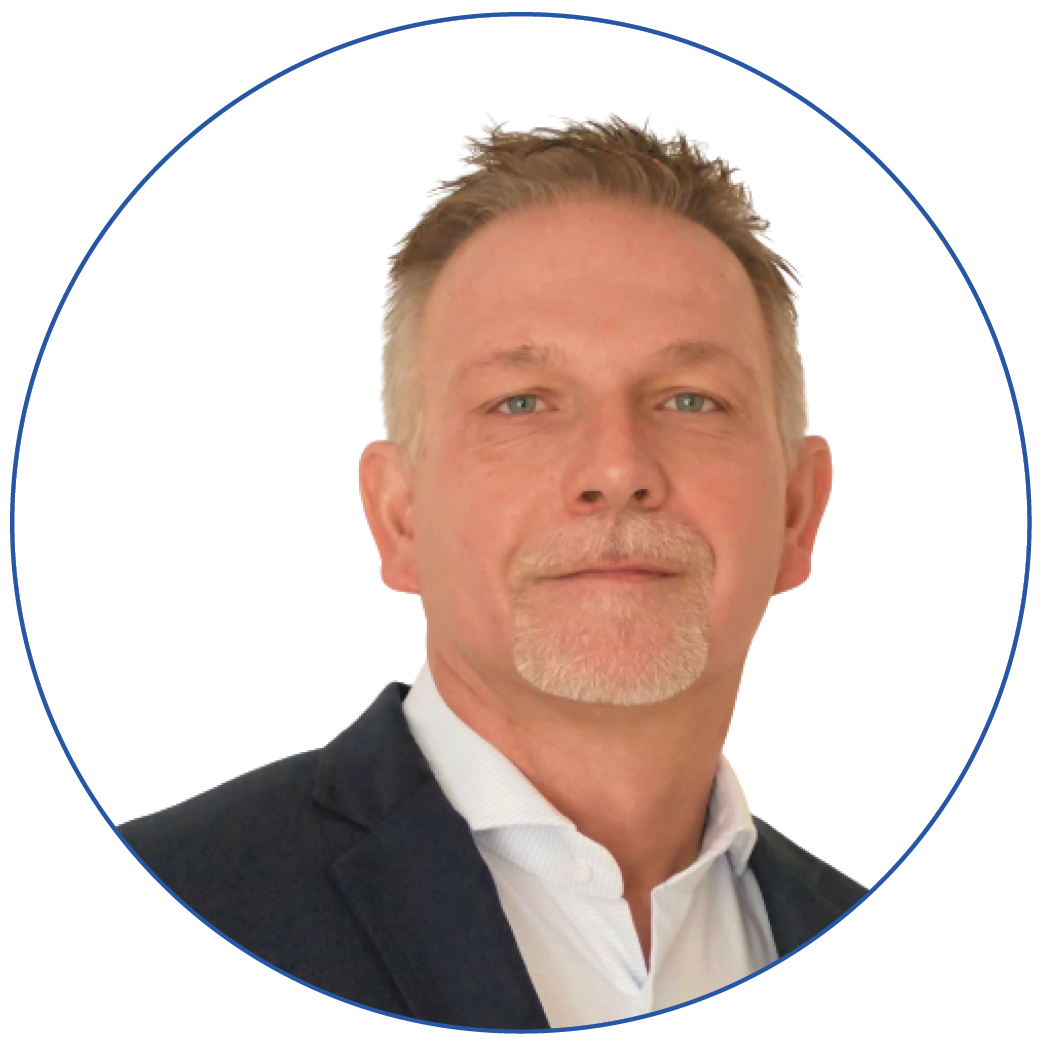
Reiner Bachthaler
Senior Product Manager
Interested? Then please feel free to contact us.
You are currently viewing a placeholder content from HubSpot. To access the actual content, click the button below. Please note that doing so will share data with third-party providers.
More Information