Author: Holger Süß
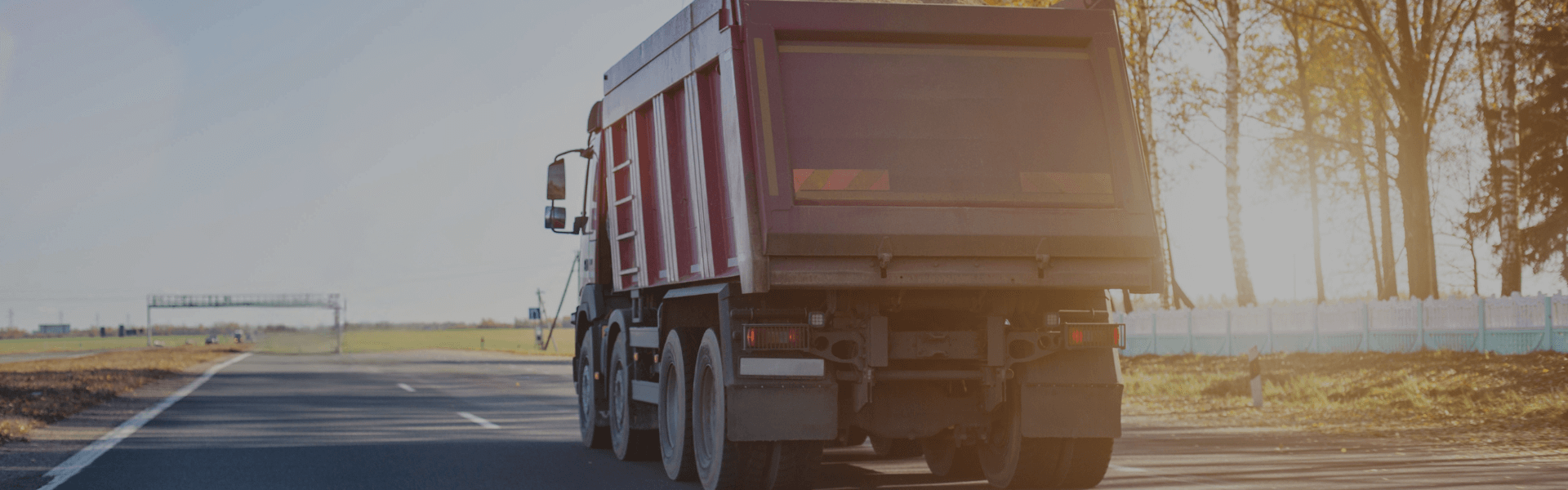
Automated truck loading for bulk materials
Unlocking process efficiency through automation
Automated truck loading in the bulk materials industry requires precise synchronization between hardware and software. Reliable weighing, dosing and conveying systems ensure accurate and consistent material loading, while sensors monitor the entire process in real time
For many companies, the integration of automated truck loading is a challenge, as their infrastructure has grown over the years and often consists of isolated machine control systems. Hardware-independent yard management software seamlessly integrates these different components, such as PLC controllers, scales and conveyor systems. This enables end-to-end digital control and step-by-step automation without having to replace existing equipments.
Additional benefits result from the real-time data exchange between yard management and control systems. This enables precise process control, automates approvals / releases, and optimizes load planning. The data will be synchronized with tThe Group ERP solution then synchronizes this data.
The impact of inefficient truck loading
Manual truck loading in the bulk goods industry causes bottlenecks, inefficiencies, and errors. Extended waiting times for each truck result in traffic jams on factory premises and prolonged idle times for logistics providers. Depending on the country, this can cost several hundred euros. In addition, idling engines increase diesel consumption, which unnecessarily increases operating costs. Manual loading is also prone to errors. Underloading results in the need for reloading or organizing and paying for additional transport. Overloading leads to the material being blown out, resulting in material losses and, above all, additional idle times of the truck in the factory. Occupational safety also suffers: more vehicle movement and manual intervention increase the risk of accidents. Delays in delivery have a direct impact on construction sites or production plants. A manually controlled process also lacks digital traceability and process control.
Hardware-independent integration into yard management software can address these inefficiencies. Existing systems don’t need costly replacements; with the right interface connection and PLC integration, they can be effectively incorporated into a digital control system with minimal modifications.
Key requirements for hardware and software solutions
Hardware solutions for automated truck handling and loading
Automating truck loading in the bulk goods industry demands dependable and accurate hardware. This equipment operates reliably even in harsh industrial environments. This includes weighing systems, bulk loading automation systems and modern sensors for vehicle positioning. In addition, QR, RFID or camera systems can be used for truck identification to ensure error-free and fast identification of the product and quantity to be loaded. In order to control the material flow seamlessly, the conveyor technology, silo control and barrier system should be controllable. A yard management system with flexible interfaces is crucial for successful integration with little effort. Existing hardware and possible additional interfaces can be flexibly integrated.
Software solutions for managing automated truck loading
An efficient Yard Management System (YMS) is the key to controlling automatic truck loading in the bulk goods industry. The YMS enables precise coordination of all processes and ensures real-time data exchange between yard management, the ERP system and the PLC-controlled loading and dosing equipment. This close integration ensures exact dosing of bulk materials and seamless operation. This eliminates material losses and incorrect loading.
With integrated control mechanisms like load status checks and automated weighing data transmission, loading is only authorized when all parameters are correct. This increases process reliability and eliminates the need for manual intervention. The open architecture of the software ensures maximum flexibility and scalability, so that it can be easily adapted to existing systems and future extensions or additional loading points can be easily integrated.
With this hardware-independent and flexible architecture, companies can modernize existing systems, automate processes, and implement comprehensive digital control of truck loading—regardless of the machines or control systems in use.
Efficient truck loading of bulk goods: silo and bag loading solutions
In the bulk goods industry, two primary methods of truck loading are prevalent. Silo loading for powdery or granular materials such as cement, sand & gravel and lime & calcium carbonate. And then there is automated bag loading, where bulk goods packed in bags are loaded onto trucks.
Both processes can be significantly optimized through automation.
Automated silo loading
Automated silo loading process
Benefits of automated silo loading
- Precise control guarantees short loading times
- Extraction technology minimizes health and environmental pollution
- Automated weighing systems prevent overloading or underloading
- Digital processes enable seamless integration into warehouse and transport management
Automated bag loading
Automated bag loading process
Benefits of automated bag loading
- Increased loading speed due to conveyor technology and robots
- Reduced personnel deployment with enhanced precision
- Safe transport through optimized loading arrangements
- Seamless documentation and error-free loading via connection to digital yard management systems
Conclusion
The future of automated truck loading depends upon smart digital connectivity and real-time integration of information. Yard management software, control technology, weight-measuring devices, and modern sensors are becoming increasingly harmoniously linked. The digital link between automated bulk loading systems, machine control, and yard management unlocks several advantages: efficient handling of material flows, less waiting times, elimination of human errors, and maximum resource optimization. Plants are choosing hardware-independent, flexible software solutions that can be perfectly integrated into existing infrastructures. This approach makes gradual automation possible without the need to invest large capital amounts in new machine control systems or conveyor technology. The combination of smart networking and flexible software offers a scalable, efficient, and future-proof automation solution.
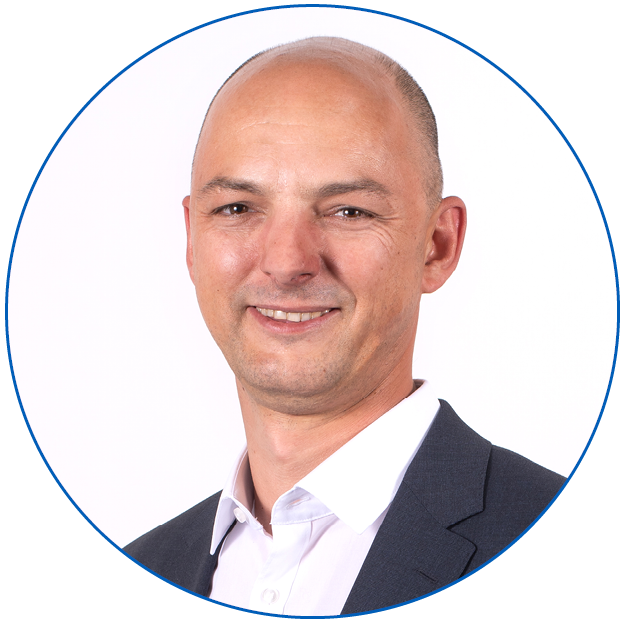
Holger Süß
Team Leader Presales & Project Management
We work with you to design a customized solution.
Let us turn your challenges into successes – contact us today!
You are currently viewing a placeholder content from HubSpot. To access the actual content, click the button below. Please note that doing so will share data with third-party providers.
More Information