Author: Reiner Bachthaler
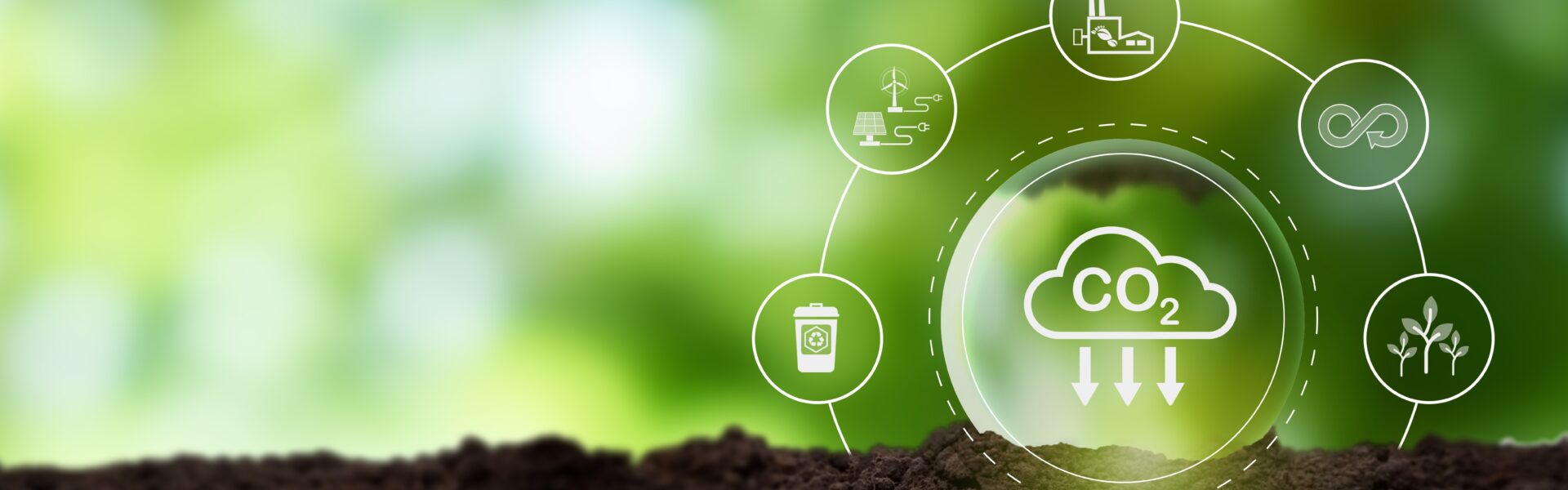
Sustainable digitalization in bulk goods logistics
The building materials industry is confronted with the constantly growing demand to improve not only its performance, but also the sustainability of its processes. Life cycle assessment and CO2 emissions are of crucial importance: customers demand comprehensible and transparent information on this. This is why both large and small and medium-sized companies are placing increasing emphasis on sustainability in their own production and logistics. Topics relating to sustainable digitalization have initially found their way into the area of highly processed products (such as cement or asphalt), readymix (such as concrete) or lime, but are also relevant for other industries such as sand & gravel.
At first glance, it may seem sensible to focus on improving sustainability in the manufacturing process of building materials. However, the considerable potential that lies in the automation and digitalization of logistics processes is often not fully recognized – a potential that can not only increase the efficiency of the entire process chain, but also significantly reduce CO2 emissions.
The challenge is to develop an effective and sustainable digitalization strategy for bulk goods logistics that involves all relevant stakeholders (customers, suppliers, freight forwarders and recipients). Key aspects include the identification of the main use cases and the consideration of project-specific factors that are crucial for successful implementation.
Optimization of the entire supply chain
Nowadays, typical logistics processes such as ordering, order and transport planning and delivery are often decentralized and assigned to the respective production sites. Planning and optimization that goes beyond the individual plants does not usually take place. In addition, there is often a break between different, non-integrated partial solutions along the process chain, i.e. there is no online data or information exchange between these systems.
The current challenges in the logistics workflow:
- Orders are often placed by e-mail (or telephone) and not online.
- Orders are not optimally distributed to the most suitable production sites; there is a lack of transparency about better alternatives.
- There is no load balancing between the various plants (where long waiting times are to be expected, which plant may have no more stocks of certain materials, etc.)
- Non-optimized transports lead to longer journeys and higher fuel consumption.
- With asphalt and readymix, there is a risk that deliveries will not arrive on time and the material can no longer be used or that the quality on the construction site is inadequate.
Options for optimization
Minimization of manual activities and delays
An inefficient logistics process is often characterized by manual, error-prone processes, media interruptions and delays. Particularly in plant logistics (such as Axians VAS Yard Management), there is considerable potential to increase efficiency and automation through the use of advanced logistics software and thus also to promote the sustainability of processes.
Currently, truck drivers often arrive at the loading site unannounced, are not always aware of the details of their cargo and have no set loading time, resulting in a manual and time-consuming sign-in process at the plant. In such a scenario, delays and backlogs are not uncommon, but rather the norm.
The efficient design of the respective process steps and immediate, digital access to the required data can significantly reduce manual work and waiting times during operation.
Typical examples:
The delivery process can be optimized and made more effective through the central coordination and announcement of deliveries and the provision of relevant information for the driver. The necessary information for loading and Delivery are already known and centralized before the truck arrives at the plant, cloud-based logistics workflowsystem – accessible to the driver via his app and in the plant’s logistics system. This eliminates the time-consuming search for delivery information and thus reduces unnecessary waiting times for the truck.
The use of self-service terminals, which are equipped with a plant logisticsogistics system such as the Axians VAS Yard Management online, the check-in process can be at the plantentrance in a matter of seconds. The truck is identified quickly – whether by cameras or other efficient recording technologies such as QR codes, TAN entries or RF/ID cards. At the terminal, the driver immediately receives information about the assigned loadingpoint. The process of loading and unloading the checkout when leaving the plant can be a automation can be significantly accelerated. This means the truck spends less time in the factory and consumes less fuel, which minimizes the ecological footprint.
One example of this is the use of mobile terminals on wheel loaders or forklift trucks, which immediately provide the operator with the correct delivery and Bloadingddata interactively. This avoids communication errors, the pressure or the manual completion of loadingbills and the time required for subsequent corrections.
These examples illustrate the variety of logistics solutions that can be used to increase sustainability in bulk goods logistics as effective decarbonization begins with in-depth process optimization.
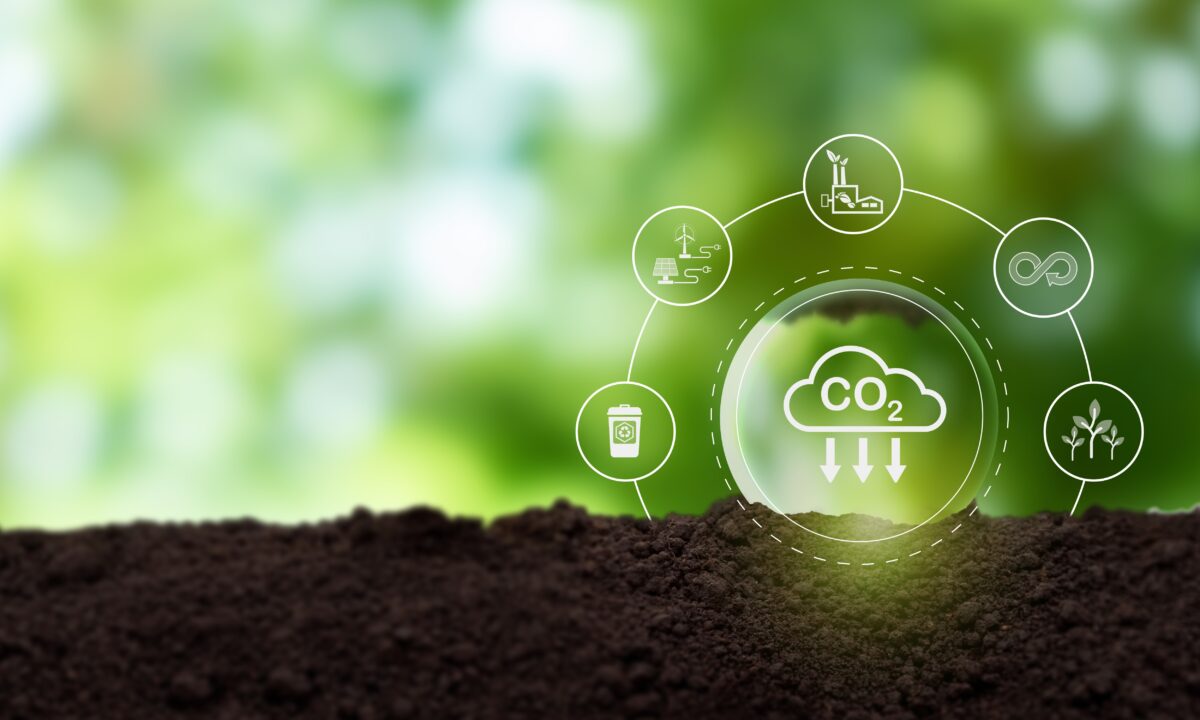
Digital and paperless logistics workflow
Current practice in bulk goods logistics is often characterized by a large number of paper-based processes, which regularly lead to media disruptions. Here are some common examples:
- Printing order lists and delivery schedules
- Printing of pre-delivery bills and loading instructions
- Multiple prints of delivery bills after loading at the factory exit
- Copying the paper-based delivery bill after manual signature by the recipient
- Manual creation and copying of driving reports by the truck driver
This results in an unfavorable CO2 balance for these logistics processes. A simple four-page print per delivery results in around 2.5 tons of CO2 for 120,000 deliveries per year. The overall potential for increased sustainability through a digital, paper-free process is undoubtedly much greater.
This achieves a paperless workflow in bulk goods logistics:
Orders are placed directly online by the customer or planner – without paperprintoutprintout – in a central, cloud-based logistics workflow system (such as Axians VAS Cloud Logistics).
Delivery time schedules are transmitted online to the transportation companies (either by accessing the same system or by transmission via web API to the carrier’s planning system).
Information on planned and allocated deliveries is sent online to a driver app, which facilitates check-in at the loading plantautomated loading and the creation of electronic delivery notes. delivery notes without outputruck made possible. The documents are also electronically in the mobile app (e.g. Axians IAS Driver App).
The recipient confirms receipt of the goods in the app, and the delivery data enriched in this way are automatically sent electronically to the recipient, the customer and the supplier’s ERP system.
The ridetreports are generated electronically in the driver app and transmitted online to the ERP system for evaluation and invoicing, e.g. via Axians VAS Cloud Logistics.
The result is a paperless workflow that significantly improves the sustainability and carbon footprint of logistics processes in the bulk goods industry, saves costs, avoids media disruptions and increases transparency for all parties involved.
Conclusion
Advancing digitalization in the field of bulk goods logistics opens up far-reaching opportunities to significantly improve both the environmental footprint and the efficiency of processes. By optimizing supply chains, minimizing manual intervention and waiting times and implementing a paperless workflow, it is possible for suppliers in the building materials industry not only to act in a more environmentally friendly way, but also to save considerable costs. Sustainable digitalization therefore not only contributes to environmental protection, but also gives companies an economic advantage over the competition.
To ensure the success of your personal digitalization project, it is crucial to choose an experienced partner like Axians IAS to implement a tailored and sustainable digitalization solution.
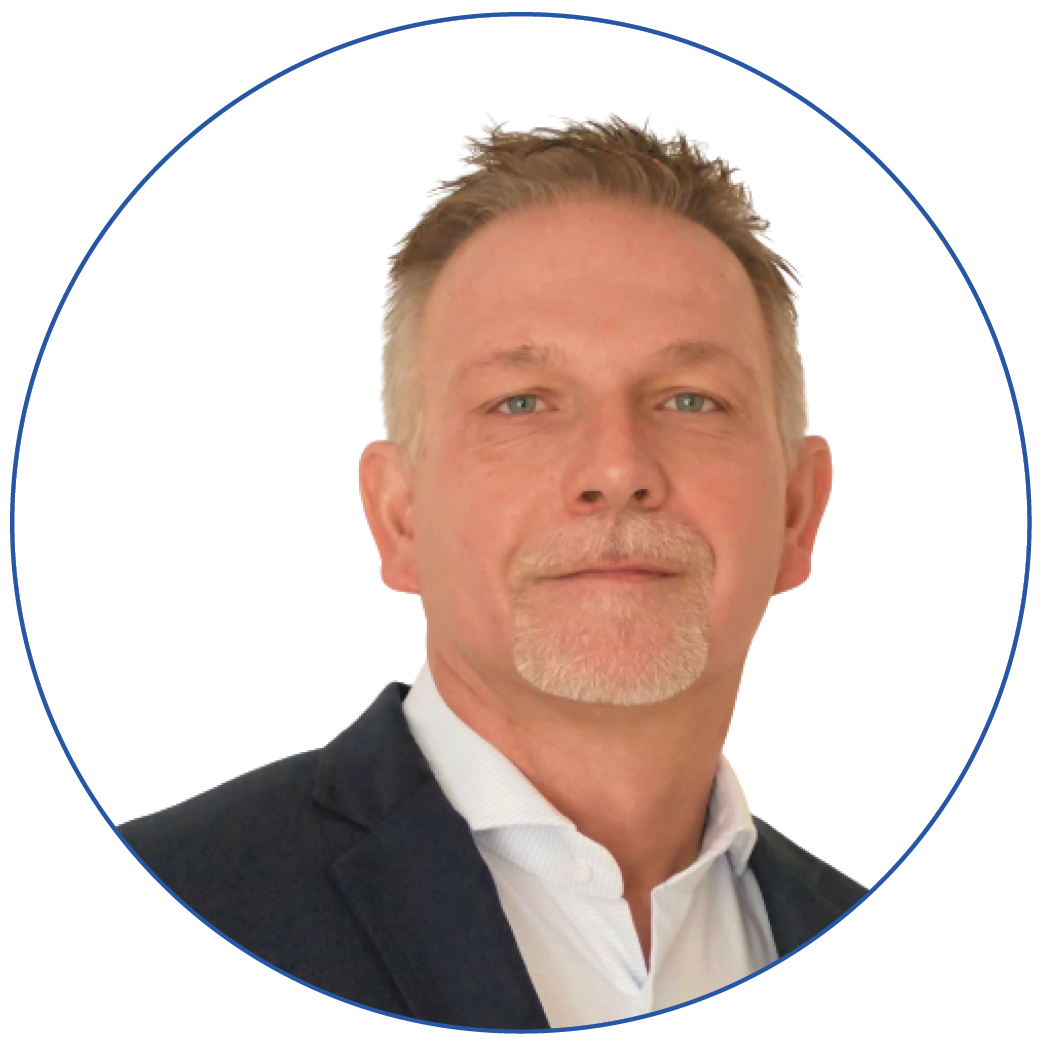
Reiner Bachthaler
Senior Product Manager
We work with you to design a customized solution.
Let us turn your challenges into successes – contact us today!
You are currently viewing a placeholder content from HubSpot. To access the actual content, click the button below. Please note that doing so will share data with third-party providers.
More Information