Author: Johannes Kokol
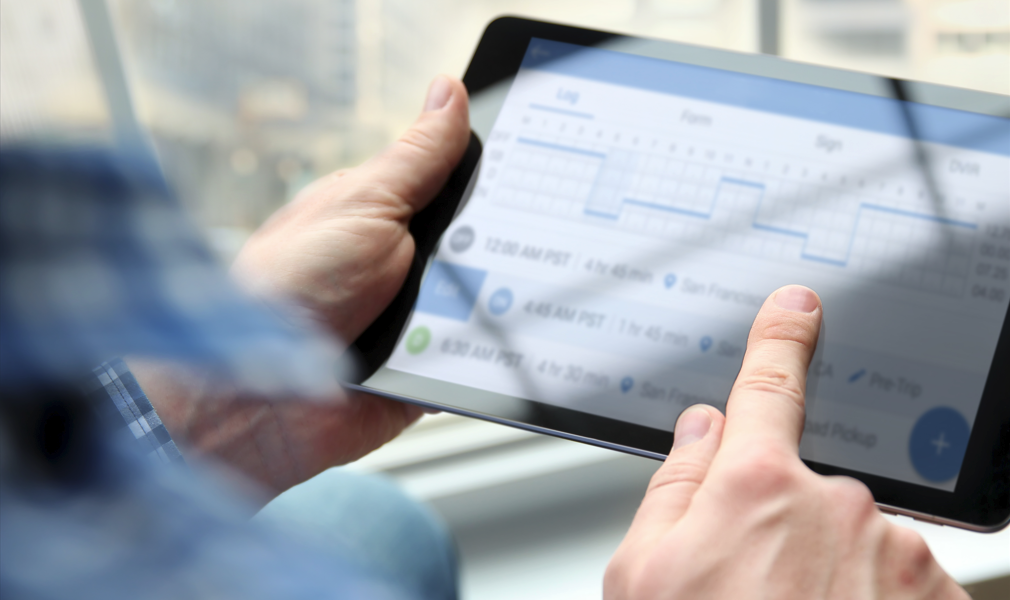
Efficient Time Slot Management and Queue Management Systems
In logistics, efficient time management for deliveries is of crucial importance. This applies not only to the bulk goods industry, but also to any company that is confronted with a high number of inbound and outbound deliveries. Efficient time management not only helps to optimize processes, but also minimizes waiting times and increases safety in the plant. By combining this with a call-out system, these goals can be achieved efficiently and effectively. This article highlights important aspects and requirements that should be considered when selecting and implementing a modern time slot management and call-out system. The entire process is considered, from initial planning and coordination in the plant through to final reporting and analysis.
Planning in advance
The highest degree of efficiency is achieved by integrating careful planning in advance. A portal (e.g. VAS Cloud Logistics) is suitable for this, in which the freight forwarder or the driver themselves can conveniently book time slots in advance. If this booking also contains information about the material to be loaded or unloaded, the distribution to the loading points can also be planned efficiently in advance. Such an intelligent system can also be of great benefit to companies with several plants in close proximity, as is often the case with asphalt or sand and gravel plants. If one plant is working at high capacity, for example, it enables flexible redistribution to another plant. This effectively distributes the load for the individual plants, avoids bottlenecks and increases overall efficiency. The integration of a central portal not only improves planning and coordination, but also increases the transparency and traceability of logistics processes. This leads to optimized use of resources and smoother handling of transport and logistics tasks overall.
Coordination in the plant
Once the trucks have arrived at the plant, they must be coordinated in the best possible way to minimize downtimes and avoid chaos in the plant. Excessive idle times are not only inefficient, they can also result in fines for hauliers. The carbon footprint of long idle times should also not be overlooked, especially in regions where drivers have to keep their engines running while waiting to use air conditioning or heating. There are various options available for coordinating the trucks in the plant, each with its own advantages and disadvantages. There is no perfect solution that can be applied to all plants, but a flexible solution is needed that can be individually adapted to the conditions on site (such as with the help of VAS Yard Management).
Waiting list management
If several charging points are available at a plant, each of these charging points should have its own waiting list. These lists must be flexibly controllable in order to take different priorities into account. This can, for example, be the classic first-in-first-out principle, but depending on the situation, vehicles with higher priority may also need to be taken into account or special distinctions made between deliveries and deliveries. If the same product is available at several loading points, dynamic re-sorting from one loading point to another can be advantageous in order to reduce downtimes. Despite the goal of fully automating the processes, it should be possible to intervene at any time and also manually influence the waiting list. When the trucks reach the plant, there are various possible processes, some of which can differ greatly from one another. For example, drivers can drive directly to a SelfService Terminal to register and receive instructions on which loading point to go to, or whether they should first drive to a waiting area (parking lot). In some cases, it makes sense not to let the trucks drive directly to an entry terminal, but to direct them to a parking lot in front of the plant first. The removal of the waiting area can increase the overview and safety in the plant and reduce the risk of accidents. After the drivers have parked the trucks, they can go to a waiting area, for example. The waiting room can then be used for registration at a self-service terminal, to display the waiting list and as a staging area. If there is no possibility of a sufficiently large waiting room, it can be helpful to install large outdoor displays in the parking lot so that drivers can see when it is their turn from the comfort of their cab. A real-time view of the standing times of all trucks in the parking lot with colored markings when certain times have been exceeded helps the delivery plants to avoid penalties (fines) to carriers. Direct notifications via SMS or app are also possible.
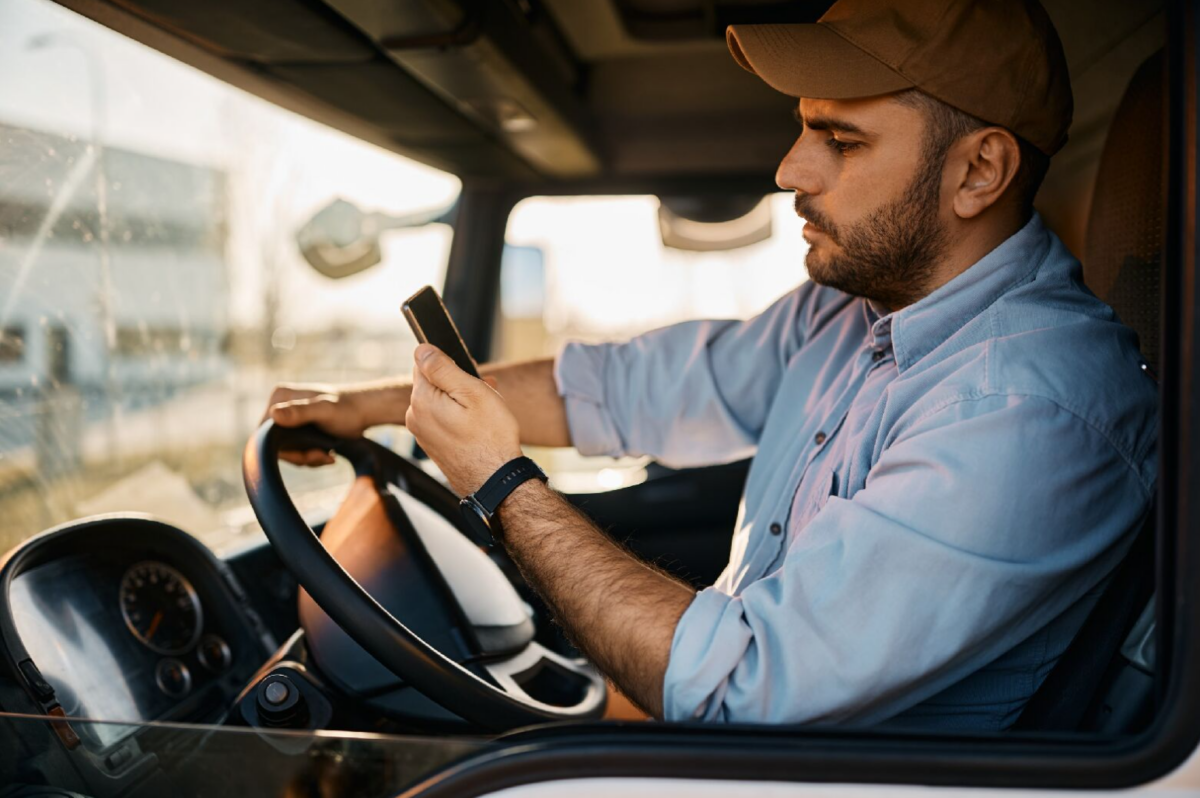
Digital apps
In many cases, it makes sense to display the waiting list digitally in an app (e.g. VAS Driver App). This has the following advantages:
Drivers can be informed in real time about their status on the waiting list. This reduces uncertainty and waiting times. Drivers are always informed exactly when it is their turn.
As soon as it is a driver’s turn, he receives a push notification with all the relevant information, such as the exact loading point.
A well-integrated app can be used directly for identification at the plant. This means that drivers no longer have to register manually at the plant, which speeds up the process considerably.
Drivers can manage all necessary documents, such as delivery bills, directly in the app. This simplifies processing and ensures paperless administration.
An app with geofencing can be a valuable addition to truck waiting list management, for example through automatic notifications as soon as the truck gets close to the plant, identification at loading points, real-time tracking and much more.
Interfaces
Ideally, waiting list management should not be an isolated solution, but should be embedded in the existing system. This often requires interfaces to carrier tools or transport management systems. These make it possible to visualize the current status and ensure transparent times, which in turn facilitates coordination and improves planning.
Reporting and analysis
In addition to coordination, time slot management should also offer meaningful reporting. Comprehensive reporting after completion of the processes is helpful in identifying peak times and improving future planning. By analysing the data, bottlenecks can be identified and measures taken to optimize them. This can be done, for example, by providing additional capacity at certain peak times. For some companies, it can be useful to offer dynamic prices based on the reporting in order to ensure that the plant is utilized as evenly as possible.
Conclusion
Efficient time slot management and sophisticated call systems are crucial for optimizing truck coordination in production plants. The combination of flexible planning, modern technology and transparent reporting can minimize waiting times, improve safety and increase efficiency. This not only leads to better utilization of resources, but also to greater satisfaction among drivers, freight forwarders and customers. The variety of requirements places high demands on a time slot management system. It should be flexible enough to adapt to different conditions and be compatible with both existing and new systems, regardless of the hardware. It should also be easy to integrate into the existing digital ecosystem.
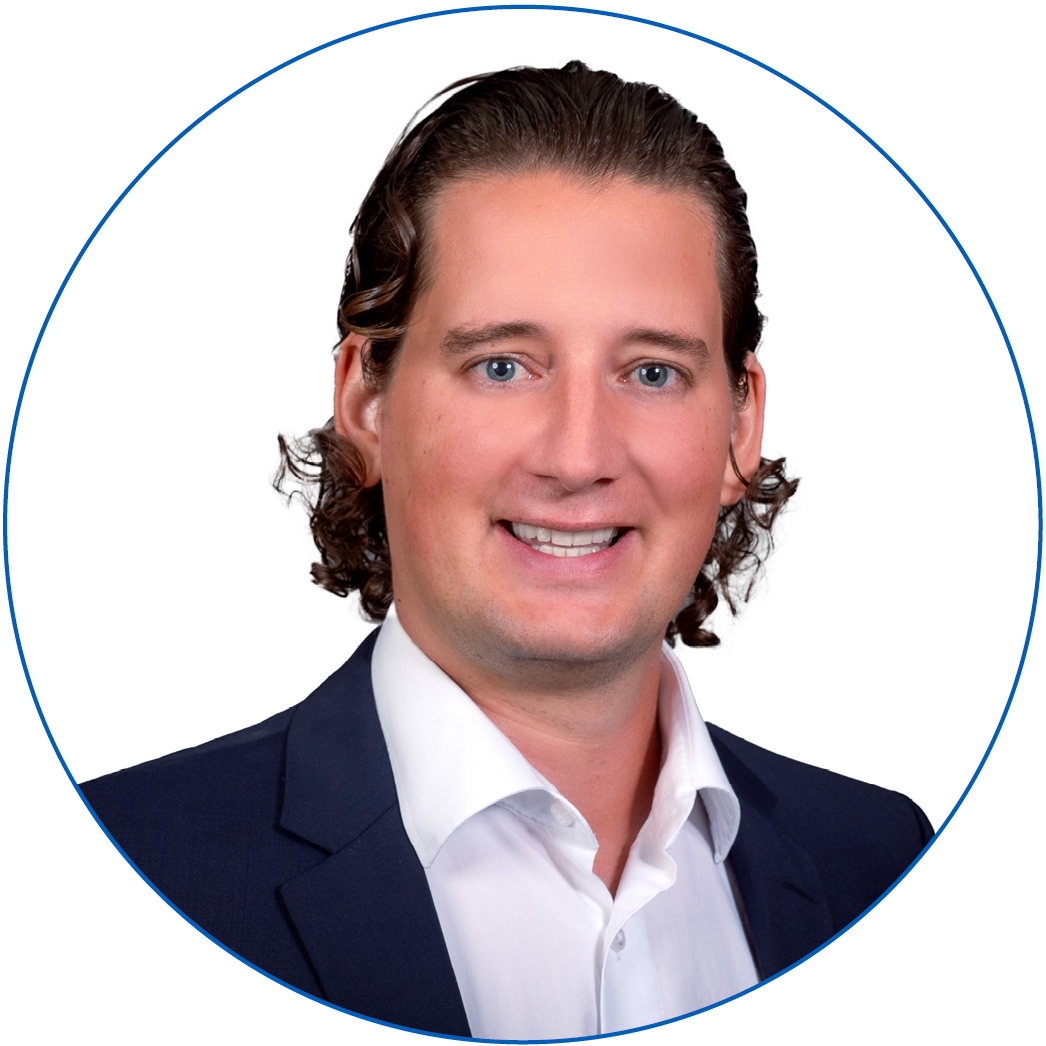
Johannes Kokol
Junior Project Manager
We work with you to design a customized solution.
Let us turn your challenges into successes – contact us today!
You are currently viewing a placeholder content from HubSpot. To access the actual content, click the button below. Please note that doing so will share data with third-party providers.
More Information